中国C919究竟有哪些技术成就,共突破五大技术难关

雷曼军事现代舰船
文|雷曼军事现代舰船
C919这款飞机固然可以称为国产大飞机,但似乎并不能反映出我国飞机制造生产技术的前进。其实并非如此,虽说C919的出先并不意味着商飞就赶上了波音空客,但确实完成了中国民用航空大飞机很多关键技术“零的突破”,集中体现在材料加工上。

表1是C919的主要系统以及大件研制单位,研制生产单位为中国公司,外国公司的部件采取的研制模式是中国单位负责性能测试、部件组装,外国公司负责提供技术支持或全套设备,因此不能称之为我国的技术突破。机身和机翼等结构的加工制造设计完全由我国公司独立完成,可称之为技术突破,主要包括以下几个方面:
首先是系统集成。大飞机制造最难、最具有挑战性的就是系统集成,也是大飞机制造的最核心技术,所谓的系统集成就是怎样搭配合理的配件让飞机整体性能最优。这就好比一台笔记本电脑,在配置完全一样的情况下,设计水平不同则往往呈现完全不同的性能表现。
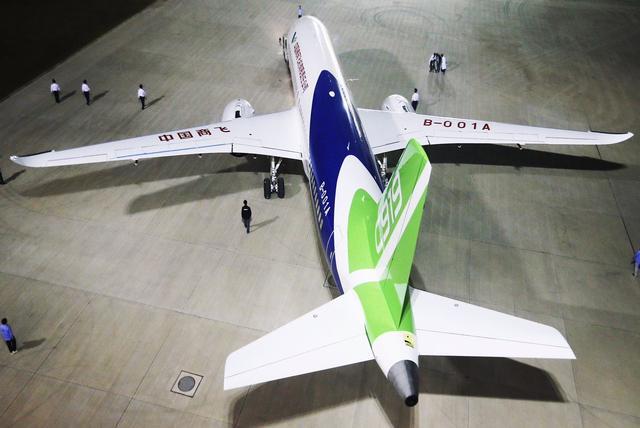
在项目资金固定的情况下,如何将各个国内外公司的系统合理的搭配在一起需要大量的设计、仿真与实验。C919的上天意味着,商飞对系统集成有了一定的突破,但并不代表集成水平已完全成熟,因为集成方法还要根据试飞和用户评价来不断优化。在各类新闻报道中可以发掘,本次商飞制造C919大量采取了网络三维制造模式,使部件设计、系统集成实现了全数字化、去图纸化,各单位研发的部件能通过网络实时共享,随时调整参数,这种系统集成方法大大降低了生产周期和设计难度,并节约了设计成本。
其次是机身合金零件集成加工。C919的前身和中后机身均由中航工业洪都公司制造,为完成制造任务,江西省与中航工业在南昌专门建造了南昌航空城,还购置了全球第二台“蒙皮镜像铣”设备。C919的前机身包括全段客舱、前货仓和再循环风扇舱,组成部件为蒙皮、长桁、地板梁、支柱、座椅导轨等共约1600多个部件,中后机身更为复杂,有同类部件约4000多个部件。
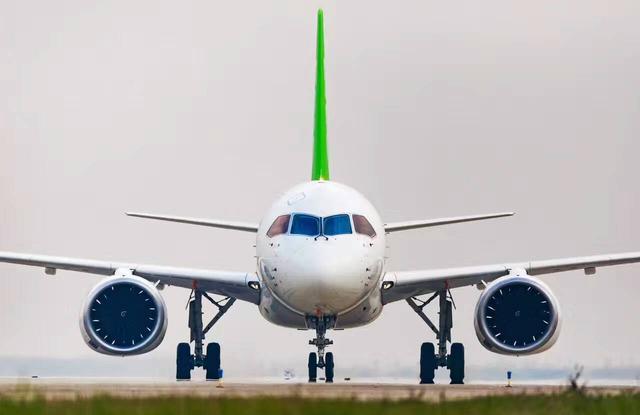
为了给飞机进行最大程度的减重,洪都集团决定使用最先进的铝锂合金材料,该材料具有低密度、高刚度、高强度和优良的温度性能等优势,但加工难度非常大,主要表现在同一材料在不同方向上的化学、物理特性有差异,如在一个长桁上平面可承受5吨的重量,在下平面则无法承受这样的重量;可塑性差,加工时极易出现断纹导致零件报废;合金不可焊接,只能进行铆接。
尽管洪都在材料上选择了当前世界上最为领先的第三代锂铝合金2196、2198、2099,且都从外国一流企业(美国铝业公司)进口,但在加工前机身工程中仍然遇到重大困难,一度出现零件加工报废率超过60%的局面,甚至有加工48件报废46件的尴尬,经费损耗更成了天文数字。通过对加工方法的改进,特别是对加工磨具结构、加热环境的一次次改进和经验积累。
最终洪都集团在加工中后机身时将零件报废率降低到了3%以下。在零件加工完毕后,如何将零件进行合理的搭配铆接又是一大拦路虎,考虑到铝锂合金的物理化学特性方向差异,必须经过大量的预先计算和安装试验、测量,工作量十分惊人。最终洪都集团在机身制造上62%部件使用锂铝合金,达到了国际一流水平。从机身的研制可以看出,这项工作对洪都集团乃至整个中国民用航空工业来说就是一次“零的突破”,制造过程中积累的系统集成和零件加工、铆接经验极大的提升了洪都集团的合金零件加工能力。
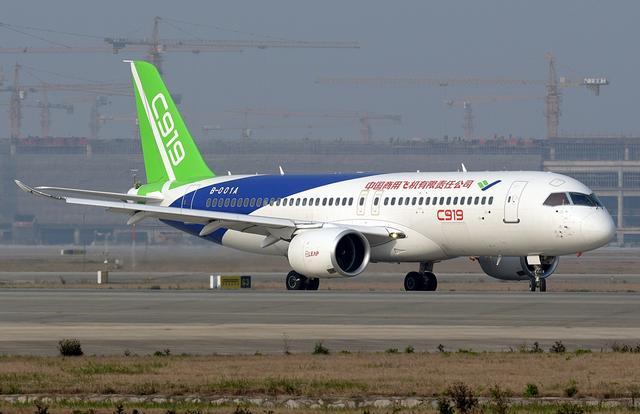
第三是中机身/中央翼的创新设计。前文提到的洪都集团只负责了前机身和中后机身的制造,而中机身和中央机翼这两个占50%的机体结构则是西飞负责完成。中机身/中央翼指飞机机翼连接的飞机机身中段和飞机机翼,C919的中机身全长5.99米,宽3.96米,由机身筒段、龙骨、应急门、中央翼等组成,含零件总数8000多个。西飞与洪都集团的思路比较一致,均广泛使用锂铝合金材料以降低飞机总重,但由于中机身段是整个飞机的载荷和操作系统中枢,因此也大量使用了钛合金和负责材料。
西飞突破的主要技术包括中央翼钛合金缘条、锂铝合金蒙皮加工,高精度复合材料铣切加工、锂铝合金钻孔、无余量装配等技术。西飞在选择机翼翼型时采用了超临界机翼,与传统机翼相比,该机翼在同等升力条件下,能使飞机的飞行速度更快。在同等的飞行速度下,能使飞机的升力更大,进而降低飞机的油耗率和巡航速度。
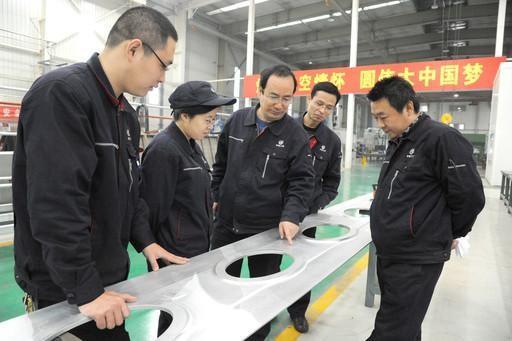
这种机翼制造起来比较困难,特别是机翼蒙皮内部有特殊要求,必须加工成台阶状。为此,西飞公司经过大量论证试验,最终选用化学铣切和五坐标激光刻形的方法攻克了技术难关,在国内实现了“零的突破”。在中央机翼设计制造方面,西飞运用在ARJ21飞机上使用过的喷丸成形法(即机床喷射高度弹丸击打材料表现加工出相应形状,类似用AK47射击钢板)攻克了飞机机翼壁板成型技术。图6即为制造成型的C919飞机机翼壁板。中央翼的副翼由西飞公司和航天海鹰(镇江)特种材料有限公司,其主要突破还是在材料的加工制作上。
第四是飞机的雷达罩实现完全国产化。该结构由中国航空工业济南特种结构研究所设计并制造,共耗时8年时间,其主要的技术突破是“四个第一”即:第一次使用泡沫夹层结构,使雷达罩的电性能更加优秀,维护更加方面经济,使用寿命更长;第一次使用全三维设计一体化,使得设计、制造均能实现同步,降低了研制难度;第一个全状态复材结构取证构型的静强度适航验证试验项目。第一个成为国内集研制、成产供应于一体的飞机结构供应商。
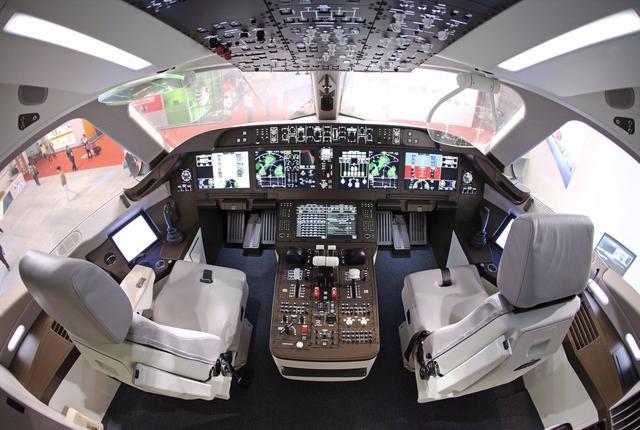
第五是飞机的轴承液压结构的设计与安装实现了突破。这两个突破由燕山大学国防重点学科实验室完成,主要是完成了大飞机各类轴承的安装与固定方法突破,液压管路的设计安装与结构设计,而这些技术以往都是掌握在国外大公司手中。
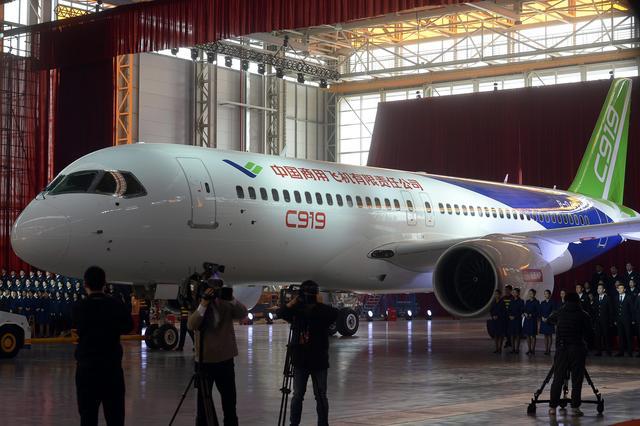
本文由军迷圈转码显示查看原文